Pull vs. Push – Learn Whether Vacuum or Compression Forming is Right for Your Production Needs
SEKISUI Voltek offers versatile solutions to your foam production needs. The best conversion method to process these foams can vary depending on a number of factors, including the size of the parts, the material used, and function, to name just a few. In today’s post, we will take a look at two converting processes – Vacuum Forming and Compression Molding – to get a better understanding of how each are completed.
The Advantages of Vacuum Forming with Volara®
The vacuum forming process begins with the heating of a plastic to its softening temperature. The crosslinked nature of Volara® allows it to be heated without melting or losing surface quality. Once the material is in its hot, flexible state, it is formed to the mold through negative air pressure and then allowed to cool. This process can be completed with sheet material in either a stationary or rotating machine, or it can be done in line with roll fed material.
Heated Through Low, Infrared Heating Systems
Because overheating the foam surface can cause the Volara® material to burn, the best results come from using infrared heating systems with percentage timers for a longer heating time at a lower temperature. A slow heat soak is generally more effective due to the insulating properties of Volara®. For in-line vacuum forming, a long conveyer oven with multiple heaters is used with the best results coming when heating the material on both the top and bottom.
Tooling Options for Vacuum Forming
Tools for vacuum forming can be made from different materials depending on the type of work. For prototyping, wood and epoxy are generally used for tooling, whereas extended run production is done with aluminum filled epoxy molds that are water cooled.
These molds need to accommodate the evacuation of air, which can be done with holes, slit channels, and/or ducts. It’s also important to consider mold proportions in thermoforming, as the draw ratio (height/diameter helps determine the necessary sheet characteristic in making effective parts.
Vacuum Forming Guidelines and Parameters
The exact parameters used for vacuum forming Volara® will depend on both the mold design and the grade of Volara® used. Mold designs should accommodate some shrinkage of the foam, which will vary based on the heating cycle and material characteristics. For designs with deeper draw ratios, the density and thickness of the foam may need to be adjusted.
Compression Molding for Producing Intricate Parts
Whether you need them molded separately or in combination with other materials like fabric, films, solid plastics, or other foams, Volara® foams have proven effective in the production of very intricate parts.
Methods of Heating Material for Compression Molding
For the compression molding process, material is usually heated with infrared heaters, although hot air ovens are sometimes used, as well. Infrared heaters can either be placed in a conveyer oven or set-up as a station on a rotary molding table. While heating times may vary depending on the thickness of the material, a longer heating time at a lower temperature is recommended for the best results.
Tooling Recommendations for Compression Molding
The molds used for compression molding can be made from various materials depending on the scope of the work you are doing. For prototype projects, molds are generally made from wood and epoxy. For extended production runs, molds are made from aluminum-filled epoxy and water-cooled metal. It’s also important to vent these molds to prevent air from being trapped during the process. The thickness and type of material used in production will determine how to separate the parts from the mold. Compression molding is completed through the use of either four-pillar or “C” type hydraulic presses with water-cooled platens.
For more information about the solutions SEKISUI Voltek can provide with the various grades of Volara® foam, please contact us.
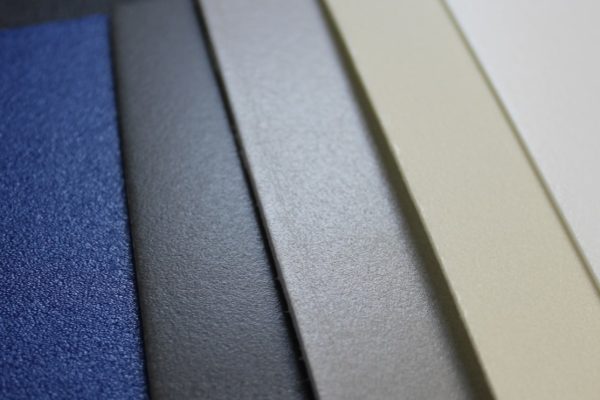